發(fā)泡制品表面出現(xiàn)白帶,即發(fā)生在和板材擠出同一方向的白色直紋,是口模和白帶對應(yīng)部分板坯和定型板面直接接觸、摩擦的表征,白帶和暗帶不同點是兩者與定型模板接觸、受到模壓程度有所區(qū)別?;疑前讕粑镩_始發(fā)生降解的表征;亮帶是板坯直接和定型接觸、摩擦的表征。
原因:
1)口模和白帶對應(yīng)截面間隙設(shè)置偏小,導(dǎo)致流量偏小,熔體從口模擠出時厚度稍微減薄,經(jīng)過定型板時未和定型板接觸摩擦出現(xiàn)的白帶。
2)物料中夾雜不潔雜質(zhì),在口模中發(fā)生滯留,導(dǎo)致熔體從口模某部位擠出時流量減少而出現(xiàn)白帶,尤其是添加不潔再生料或組分復(fù)雜、穩(wěn)定劑欠缺的再生料過多,熔體從口模某部位擠出時產(chǎn)生滯留。若白帶問題處理不及時,隨時間延長,白帶將逐漸轉(zhuǎn)變成淺灰?guī)c黑帶。
3)擠出機控制溫度不當(dāng),未使用螺桿溫控裝置,物料在擠出機、合流芯或口模擠出時截面溫度不均衡,發(fā)生局部微降解、粘料,熔體從口模擠出時,在口模某部位流速少出現(xiàn)白帶。經(jīng)實踐驗證:這和一些企業(yè)采用的3區(qū)溫度、4區(qū)、5區(qū)、合流芯溫度逐漸升高有一定對應(yīng)關(guān)系。
4)擠出機、合流芯或口模某部位存在滯留區(qū),導(dǎo)致口模某部位流量減少,出現(xiàn)白帶。
5)混合料未達到混料溫度即出料,或混料未按規(guī)定程序與單堝混料量超標(biāo),致使混料組分不均,熔體從擠出機擠出產(chǎn)生流動速度紊亂。
措施:
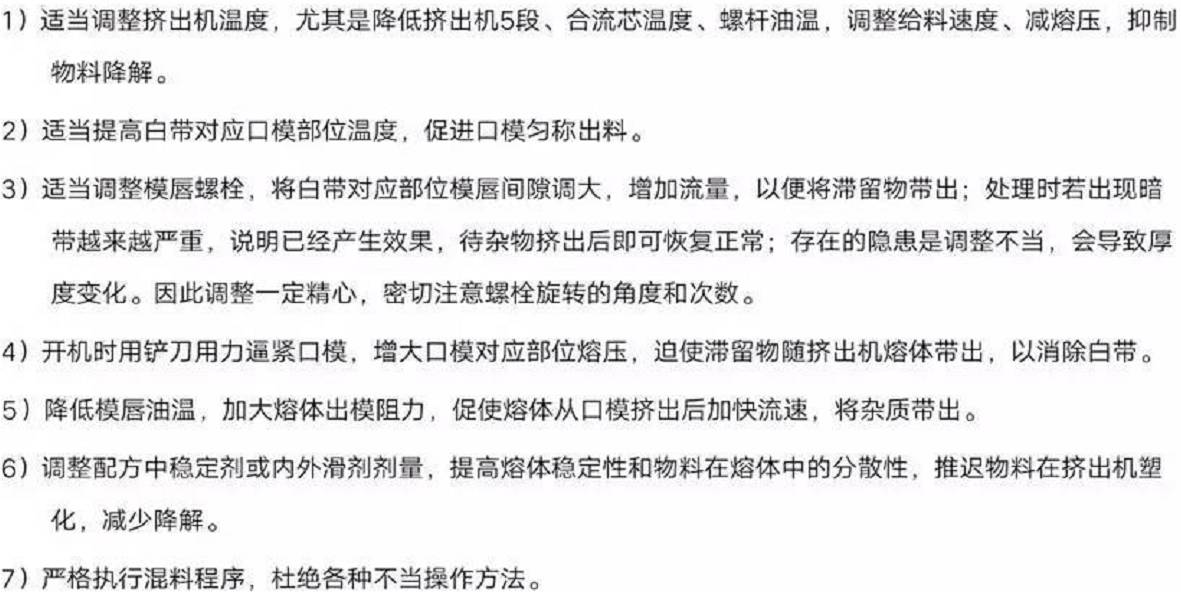
以上七項處理措施中第一、二、七項是事前預(yù)防措施,第三、四、五、六項是應(yīng)時處理措施。當(dāng)開機時出現(xiàn)白帶,一般都是口模間隙或溫度設(shè)定不當(dāng)造成的,及時處理即可見效;當(dāng)開機一段時間,發(fā)生白帶,基本上是合流芯、口模腔、擠出機內(nèi)發(fā)生滯留物造成的,如采用調(diào)整??陂g隙和溫度方法無效,應(yīng)及時停機,千萬不可盲目持續(xù)調(diào)整,以免延工誤時,造成更大浪費。停機后認真檢查口模、合流芯中是否黏附滯留物,如未發(fā)現(xiàn)異常,需進一步檢查螺筒中是否黏附滯留物并調(diào)整擠出機軸向與徑向間隙。
大量實踐驗證,處理白帶有一定時效性,若處理不及時或由白帶演變未灰?guī)В蜁ヌ幚砹紮C。處理時應(yīng)對擠出機螺桿磨損和裝置情況及近期工藝設(shè)置變動情況了如指掌,以便有的放矢應(yīng)對處理。
亮帶是由于口模間隙調(diào)整不當(dāng),導(dǎo)致亮帶處物料從口模擠出時速度增快,與口模發(fā)生直接摩擦所致,比較容易解決,適當(dāng)調(diào)小模唇對應(yīng)亮帶部位間隙即可。
可能有人認為:板材某部位出現(xiàn)白帶并非密度低所致,出現(xiàn)亮帶也并非密度高所致,依據(jù)是凡是白帶對應(yīng)口模位置熔體,出定型模板后,比周圍部位厚一些;亮帶對應(yīng)口模位置熔體,出口模后,比周圍部位薄一些。故處理白帶采取緊模口方法,處理亮帶松模口方法。其實處理措施恰好相反。凡是密度低的部位,經(jīng)過定型模板時,未和定型模板緊密接觸,得不到充分冷卻,收縮量小,而周圍密度高部位熔體,經(jīng)冷卻后出現(xiàn)表面收縮,并在定型模板壓力作用下,有向白帶部位移動傾向,而經(jīng)冷卻出定型模板后,白帶部位就稍顯厚一些;凡是密度高部位,熔體經(jīng)過定型模板時,和定型模板接觸緊密,冷卻充分,收縮量大,并在定型模板壓力作用下,有向周圍密度低部位移動傾向,因此經(jīng)冷卻后,出現(xiàn)亮帶的部位就稍顯薄一些。
發(fā)泡板材易拉斷等質(zhì)量缺陷原因和處理措施:
原因:發(fā)泡板材生產(chǎn)中被拉斷主要因素是:熔體塑化不良;強度差;操作不當(dāng)、牽引速度過快或過慢,熔體通過口模和定型板時承受的壓力或阻力過大;碳酸鈣過量;再生料穩(wěn)定性差、添加量過大;上料罐斷料等導(dǎo)致的流動速度紊亂等。
措施:

發(fā)泡板材厚度厚薄不均質(zhì)量缺陷原因和處理措施:
原因:熔體塑化不好與出模速度差異大,或模腔、合流芯黏附了大量析出物造成的。一般是板面出現(xiàn)白帶、泡孔的后發(fā)結(jié)果。
措施:
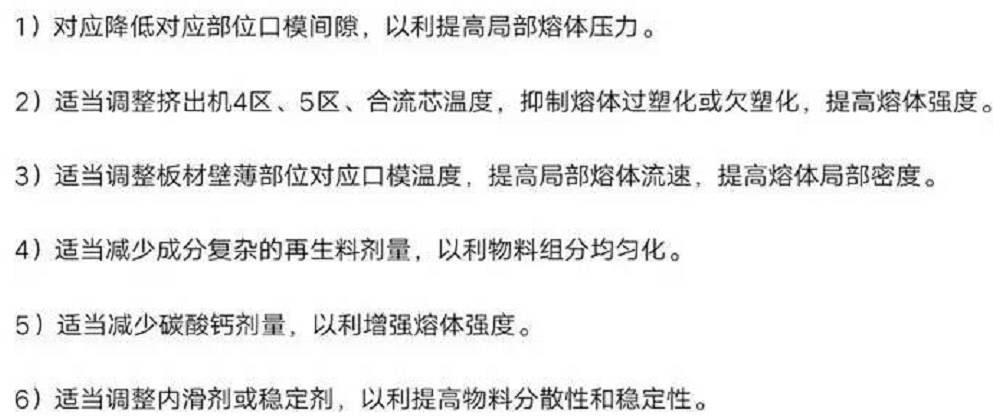
影響板材密度的因素與降低熔體密度質(zhì)量缺陷原因和處理措施:
影響發(fā)泡板材密度因素很多,既有發(fā)泡劑、發(fā)泡調(diào)節(jié)劑、穩(wěn)定劑、碳酸鈣、潤滑劑等原材料添加不當(dāng)?shù)确矫嬉蛩?,也有擠出溫度、熔壓、牽引速度、口模與定型模板之間間隙、模芯和模唇溫度、定型模板之間間隙等設(shè)置不當(dāng)?shù)裙に嚪矫嬉蛩?。從理論上講,降低熔體密度有兩大措施:一是添加發(fā)泡劑必須有足夠的發(fā)泡體積和適宜的強度,二是定型模板提供的空間應(yīng)和發(fā)泡體積相適宜,兩者之間能夠相互平衡。如果發(fā)泡體積不足,定型板提供空間過大,即發(fā)泡體小于定型板提供發(fā)泡空間,板面則會不平整。反之發(fā)泡數(shù)量過大,定型板提供空間過小,即發(fā)泡體大于發(fā)泡空間,隨發(fā)泡體承受熔壓增加,則會影響發(fā)泡,密度相應(yīng)也會偏高;調(diào)節(jié)劑添加量過多,雖然能減少破孔,提高密度,但如果過量容易使發(fā)泡困難,影響發(fā)泡。
措施:
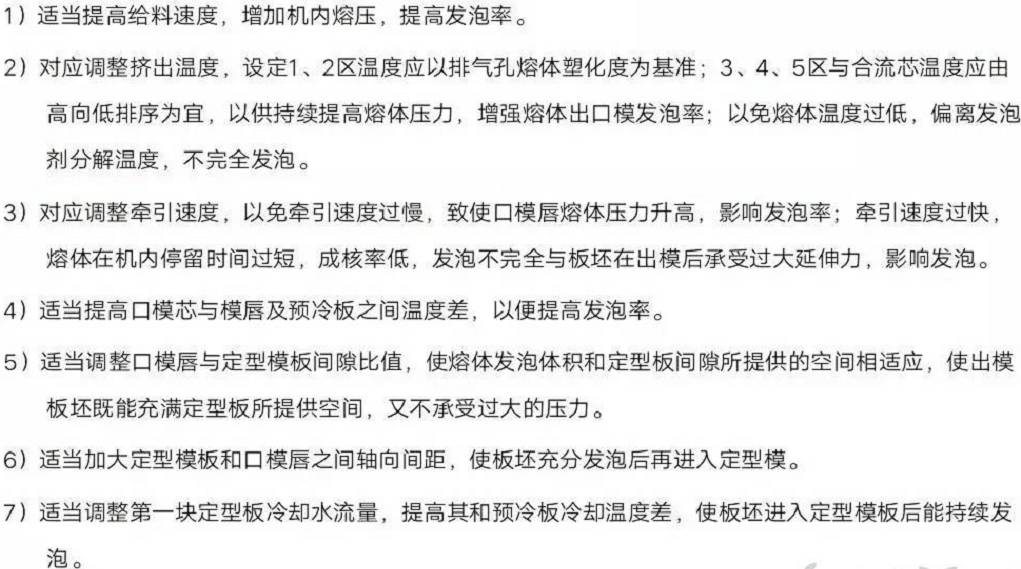
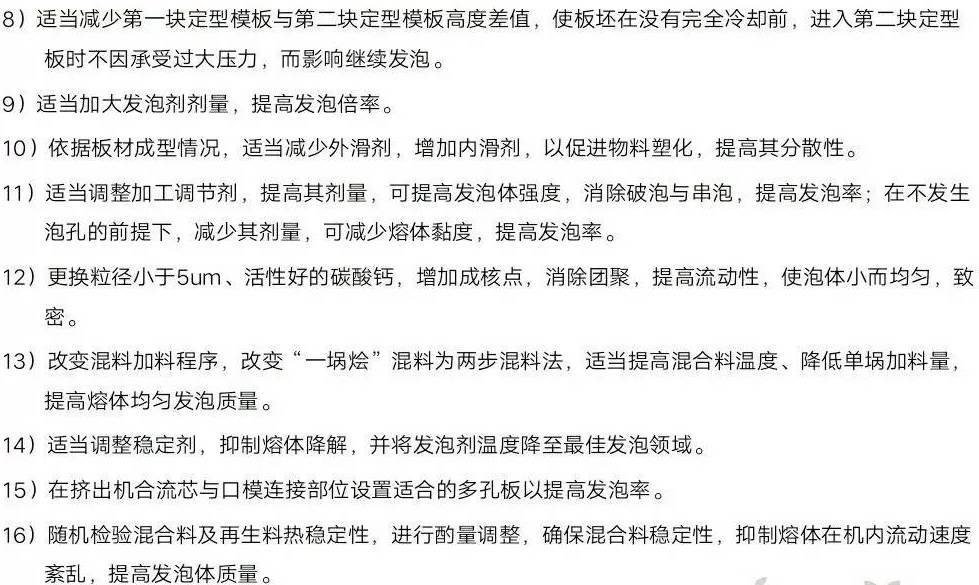
調(diào)整時應(yīng)根據(jù)生產(chǎn)所需板材質(zhì)量要求,按照程序由簡到繁,由工藝到配方,由減量到加量進行逐項對應(yīng)調(diào)整。值得注意的是:調(diào)整提高發(fā)泡率,降低板材密度時應(yīng)按生產(chǎn)發(fā)泡板的需要各有側(cè)重。以上許多調(diào)整措施,譬如調(diào)整措施4)5)7)8)等都是以犧牲結(jié)皮硬度和光亮度等情況,不可過之而不及,僅僅為降低密度而不考慮結(jié)皮硬度和光亮度。
影響塑料發(fā)泡板出現(xiàn)波浪紋、云紋、橫向和豎向條紋質(zhì)量缺陷原因和處理措施
因素:主要和定型板壓力、口模出料不穩(wěn),擠出速度與牽引速度之間相互不匹配等綜合因素相關(guān)。譬如熔體從口模擠出后,進入定型模板阻力過大,會發(fā)生褶皺或波浪紋;熔體出口模局部出料快,在模板整體壓力作用下,則會形成小波浪;牽引速度過慢時,在模板整體壓力下,則會形成大波浪;熔體板坯從口模擠出后局部流速不穩(wěn),在定型模作用下會產(chǎn)生云紋; 板坯從口模擠出速度過快或牽引速度過慢,板坯進入定型模時受到橫向擠壓,則會形成橫向條紋;在同樣牽引速度條件下,熔體從??跀D出局部出料速度不穩(wěn),口模出料多部分熔體進入定型模后,受到豎向擠壓,則會形成豎向條紋。
措施:
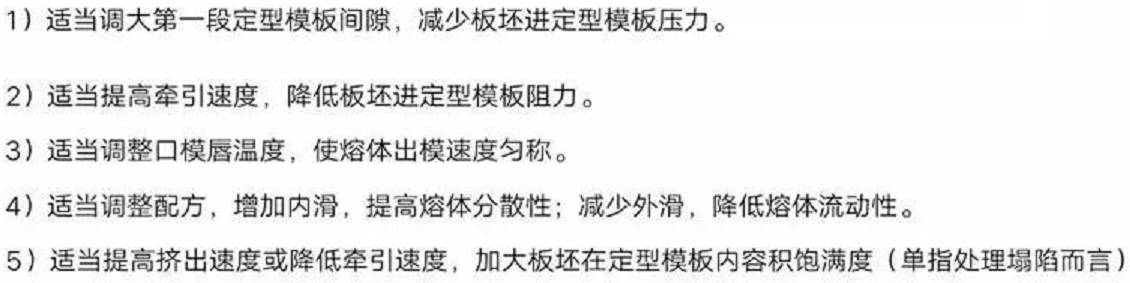
發(fā)泡板糊料質(zhì)量缺陷原因和處理措施:
糊料,即板材表面局部出現(xiàn)變色、燒焦癥狀。一般發(fā)生在密度較高的薄板上,也是發(fā)泡體黏度與阻力過大的副產(chǎn)物。隨發(fā)泡劑調(diào)節(jié)劑量增大,發(fā)泡率降低,口模唇間隙減少,熔體流動阻力增大,熔體在某部位發(fā)生局部堵料、滯留,便會產(chǎn)生糊料。凡是影響熔體流動性和穩(wěn)定性因素都和糊料有直接關(guān)系。糊料一般發(fā)生在口模,與發(fā)生在定型模內(nèi)析出有所不同。
熔體在擠出過程中因混合料穩(wěn)定性差,各段溫度設(shè)定或控制不當(dāng),發(fā)生分解;或擠出機磨損嚴重,合流芯、口模腔存在滯留料黏附等原因發(fā)生糊料。
措施:
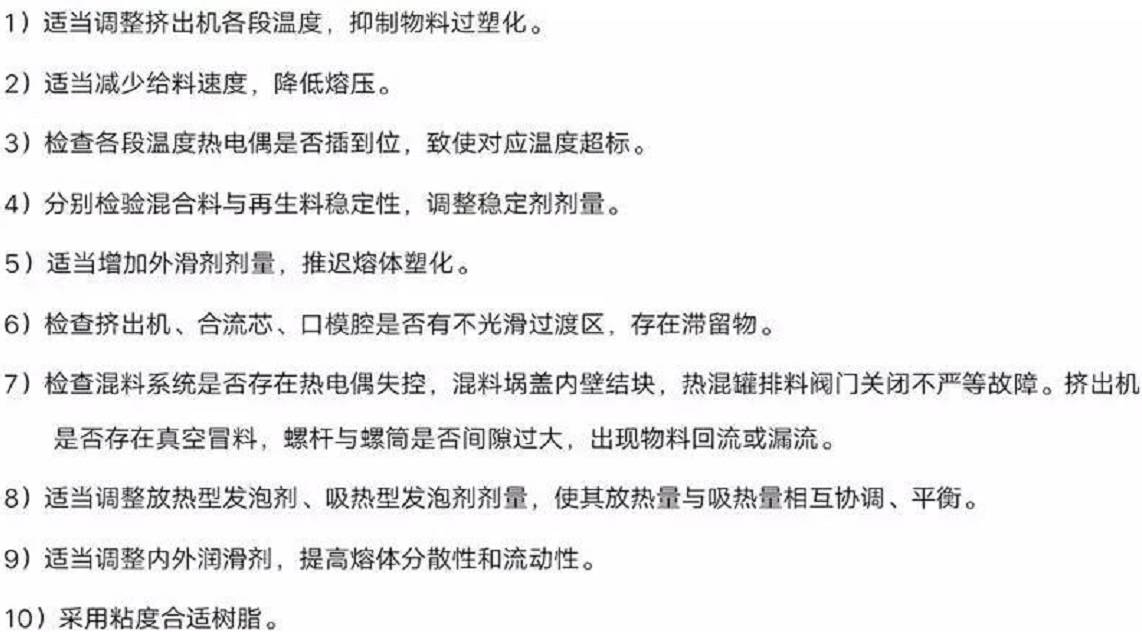
發(fā)泡板芯層強度低質(zhì)量缺陷原因和處理措施:
原因:由于結(jié)皮發(fā)泡板熔體從口模擠出后經(jīng)過充分冷卻,口模與定型模板間隙值和第一塊定型板與第二塊定型板間隙差偏大;口模油溫與預(yù)冷板及第一塊定型板水溫差偏大等原因?qū)е陆Y(jié)皮發(fā)泡板皮層硬度高,從而將同樣密度發(fā)泡板大多數(shù)泡孔集中到芯層,導(dǎo)致芯層密度、強度及硬度偏低。
措施:
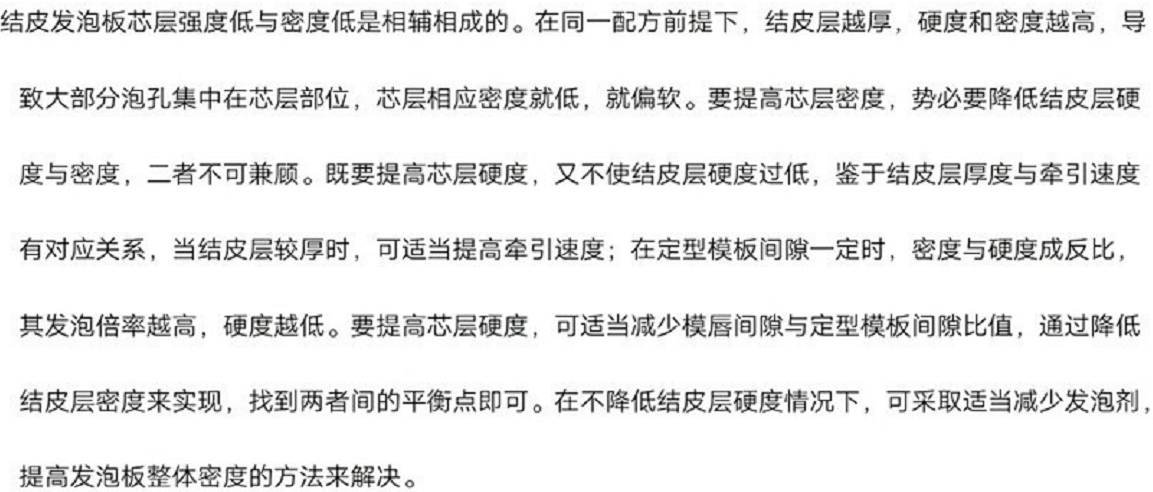
發(fā)泡板出現(xiàn)雜質(zhì)和黑色斑點質(zhì)量缺陷原因和處理措施:
原因:
1)再生料落地,回收不潔。
2)再生料中摻雜有糊料。
3)擠出生產(chǎn)過程中排氣孔中出現(xiàn)冒料未及時處理。
4)混合料未進行封閉存放。
措施:

發(fā)泡板出現(xiàn)劃痕質(zhì)量缺陷原因和處理措施:
原因:主要是熔體在加工過程中,熔體經(jīng)過時被擦傷所造成的,或混合料中混雜有鐵屑等硬性物質(zhì),將合流芯與模具表面劃傷。
措施:
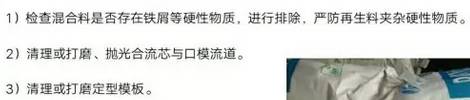
發(fā)泡板出現(xiàn)扭曲、不平整質(zhì)量缺陷原因和處理措施:
翹曲度是結(jié)皮發(fā)泡塑料板材一項重要外觀質(zhì)量指標(biāo)。QB/T2463.2-1999行業(yè)標(biāo)準規(guī)定:當(dāng)板材厚度大于5mm時,其翹曲度應(yīng)小于或等于10mm/m(毫米每米);當(dāng)板材厚度小于5mm時,其翹曲度應(yīng)小于或等于5mm/m(毫米每米)。但對于櫥柜、酒柜、衛(wèi)生潔具等家具而言,一些微小翹曲,在大面上將會導(dǎo)致家具嚴重走形,因此企業(yè)一般對翹曲度的檢驗要求也比較嚴格。
原因:主要是板材熔體內(nèi)聚集的應(yīng)力不均造成的。生產(chǎn)時在定型模板和牽引裝置冷卻、定型、拉伸約束下,體現(xiàn)不出來,但在牽引以后,熔體處于自由狀態(tài)時,其內(nèi)應(yīng)力得以釋放,才會以翹曲變形形式表現(xiàn)出來。結(jié)皮發(fā)泡塑料板翹曲變形主要表現(xiàn)在橫向與縱向兩個方向。其中橫向翹曲變形主要是口模橫向給料量或溫度設(shè)定不均及口模油路、定型模板水路局部堵塞,板材橫截面油冷及水冷不均所致,由給料多、熔壓大、溫度高的一面向給料少、熔壓小和溫度低的一面彎曲;縱向翹曲變形主要是擠出機徑向和軸向間隙偏大,致使擠出過程中螺桿在熔體作用下,向上偏移,進入合流芯與口模下部的熔體偏多;口模分流錐分流不均、口模溫度設(shè)置不當(dāng)、口模與定型模上下不對中等原因,致使出口模熔體偏流嚴重;口模與定型模相互不在一個水平線上,由受力大一側(cè)向受力小一側(cè)彎曲;各道定型??v向上下冷卻不均,由溫度高一面向溫度低一面彎曲。
結(jié)皮發(fā)泡塑料板發(fā)生翹曲變形的原因雖然簡單,但由于板面幅寬較大,且PVC流動性較差,微小應(yīng)力不均都會從板面平整度上體現(xiàn)出來,因此出來難度較大,調(diào)整的“度”很難把控。為了使整個橫向熔體出料均勻一致,在設(shè)定和調(diào)整口模橫向間隙和各區(qū)溫度時,需要根據(jù)PVC的流動性,隨偏離口模中心距離大小,口模間隙和溫度逐次提高,但也要防止“矯枉過正”。假如口模唇中間間隙過小或口模唇兩側(cè)間隙過大與口模唇中心溫度偏低,兩側(cè)溫度偏高,中間熔體流速過低,兩側(cè)熔體流速過高,亦會產(chǎn)生板材中間低、兩側(cè)翹曲的現(xiàn)象。
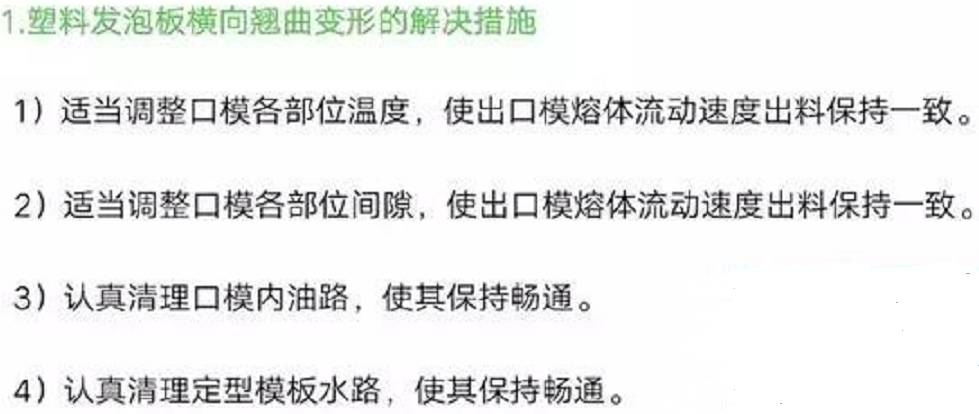
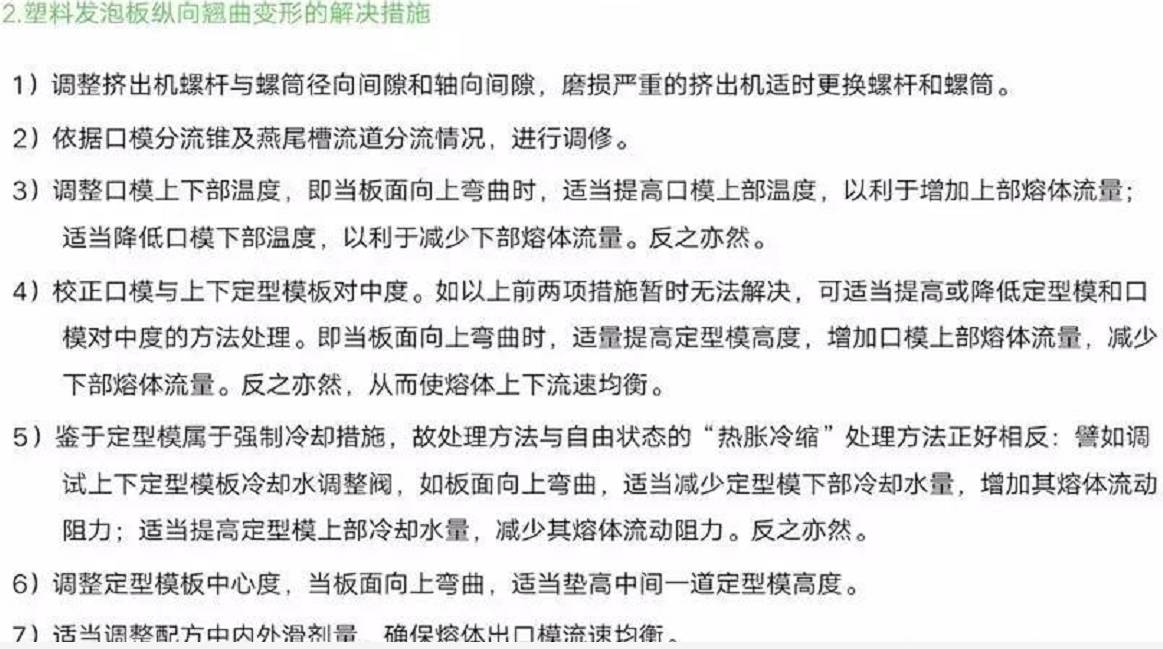
在擠出機與合流芯連接部位設(shè)置多孔板,以調(diào)整、均衡擠出口模的熔體壓力。多孔板的設(shè)置應(yīng)以擠出型坯具有足夠的熔壓為準繩,控制好多孔板的孔徑與孔數(shù)。孔排列要緊湊、均勻,流通截面約占多孔板總面積的50%-70%,板壁不宜太厚。設(shè)置多孔板僅僅是為了恒溫時,多孔板的流通截面空間可取上限,以減少多孔板的反作用力。
板面在生產(chǎn)時發(fā)生彎曲大部分原因都是擠出機徑向或軸向間隙磨損過大或口模分流錐、燕尾型分流道磨損后分流不均所致。正確解決措施應(yīng)從兩方面著手處理。對于擠出機新安裝螺桿與螺筒及新進口模一定要嚴格驗收,防范不合格產(chǎn)品投入生產(chǎn),以便把事故隱患消滅在萌芽狀態(tài)。除設(shè)置多孔板外,其他處理措施均是機械應(yīng)急措施。在處理彎曲故障時,各種措施一定要綜合利用,不可過多單用某一種措施,以免調(diào)整過量。同時以上處理措施勢必會給板材增加一定內(nèi)應(yīng)力,是以犧牲板材內(nèi)在質(zhì)量保證外觀質(zhì)量的不妥之舉,建議盡量不用或少用。
總結(jié):以上各類發(fā)泡板盡管質(zhì)量缺陷表現(xiàn)形式各異,譬如出料不均形成的各類缺陷,所采取處理措施都有一定的共性,只不過處理程序和幅度有所不同;在一個相互依存、制約的生產(chǎn)系統(tǒng)內(nèi),它們之間也存在一個相互作用和制約關(guān)系。譬如泡孔、密度、不平整等質(zhì)量缺陷,都和熔體黏度、流動性、阻力大小有關(guān)。若熔體黏度過低,局部熔壓不均,會引發(fā)泡孔,并使板材密度升高;黏度過高,會使泡孔發(fā)得很小,亦會影響板材密度與流動性,使板面不平整;口模唇間隙大,擠出阻力小,有利于穩(wěn)定生產(chǎn),但會使板材密度升高;口模唇間隙小,熔壓高,會降低板材密度,但隨擠出阻力增加,亦會影響其流動性,易使板面不平整。解決某一項質(zhì)量缺陷,必須兼顧、防范與其相關(guān)的另一項質(zhì)量缺陷,不可矯枉過正,顧此失彼。應(yīng)通過生產(chǎn)實踐,反復(fù)摸索,尋找質(zhì)量缺陷之間平衡點和臨界點,在不影響板材相關(guān)質(zhì)量缺陷的前提條件下,掌握好調(diào)整的“度”,較好解決某一個質(zhì)量缺陷。根據(jù)發(fā)泡板材厚度、密度要求和各類制品質(zhì)量缺陷對應(yīng)關(guān)系,分別采取不同措施:即采用不同配方、口模與工藝,實施按需分配,微量調(diào)整,平衡配置,則是綜合解決以上各類問題的最佳方式。
青島賽諾化工有限公司專業(yè)從事聚乙烯蠟,EBS以及硬脂酸鋅的生產(chǎn)和銷售,供應(yīng)各種氧化聚乙烯蠟,聚丙烯蠟,EVA蠟,茂金屬蠟,DBM,SBM,尼龍,EBS ,硬脂酸鋅以及聚乙烯蠟。
相關(guān)產(chǎn)品:賽托蠟、低聚物、聚乙烯蠟、EBS、光亮分散潤滑劑、環(huán)保穩(wěn)定劑專用蠟、硬脂酸鋅、抗氧劑、氧化聚乙烯蠟
文章來源:青島賽諾 編輯:青島賽諾
版權(quán)所有,轉(zhuǎn)載請注明出處:www.xyssdzrmzf.com